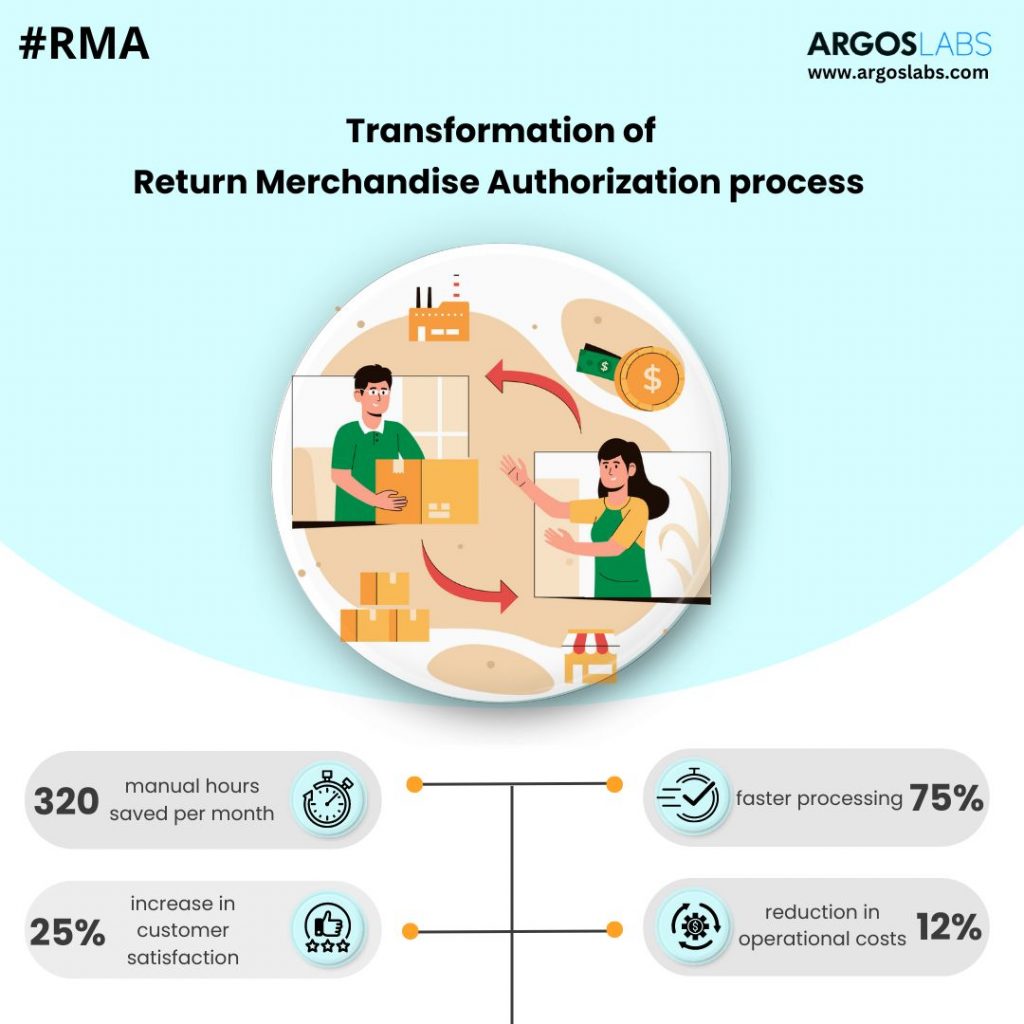
Overview
Argos Labs collaborated with a leading Global Network Equipment Provider to revolutionize their Return Merchandise Authorization (RMA) process. The provider sought to enhance customer satisfaction, reduce operational costs, and improve inventory management.
Challenge
The manual RMA process was marred by inefficiencies, resulting in:
- Delayed returns processing
- Increased customer dissatisfaction
- Higher operational costs
- Inefficient inventory management
Objective
Argos Labs aimed to integrate Email, ERP, CRM, Warehouse Management Systems, Production Management, and Logistics to:
- Automate RMA workflows
- Enhance customer experience
- Reduce operational costs
- Improve inventory accuracy
Solution Implementation
The comprehensive solution involved:
- Automated RMA Portal Development: A user-friendly portal for customers to submit returns and track status.
- Email Integration: Automated email notifications for customers and internal stakeholders.
- ERP Integration: Real-time updates for return orders and inventory management.
- CRM Integration: Customer interaction tracking and proactive communication.
- Warehouse Management System Integration: Efficient returns processing and inventory updates.
- Production Management Integration: Seamless repair and replacement workflows.
- Logistics Integration
- Streamlined return shipping and tracking.
Results
The integrated RMA system yielded remarkable improvements:
- 320 Hours Saved: Manual hours reduced by 320 per month (60% reduction).
- 75% Faster Processing: RMA processing time decreased by 75%.
- 25% Increase in Customer Satisfaction: Enhanced support and proactive communication.
- 12% Reduction in Operational Costs: Automated workflows minimized errors and increased productivity.
- 99.5% Inventory Accuracy: Real-time updates ensured accurate stock levels.
Benefits
The transformed RMA process brought numerous benefits:
- Enhanced customer experience through timely updates and proactive communication.
- Improved operational efficiency through automation and reduced manual labor.
- Increased inventory accuracy, reducing stock outs and overstocking.
- Better decision-making through real-time data analytics.
Conclusion
The Global Network Equipment Provider’s initiative to automate the RMA process with Argos Labs resulted in significant operational efficiency gains and enhanced customer satisfaction. By streamlining returns processing, the provider strengthened its customer-centric approach and reinforced its position as a leader in the global network equipment market. This case study demonstrates the potential for integration and automation to drive business excellence and customer delight in the technology sector.
About Argos Labs
Argos Labs is a leading provider of innovative solutions, empowering businesses to achieve operational excellence and customer satisfaction. Our expertise in integration, automation, and digital transformation enables organizations to thrive in today’s competitive landscape.